Addressing Challenges In Automated Visual Inspection Of Lyophilized Vials
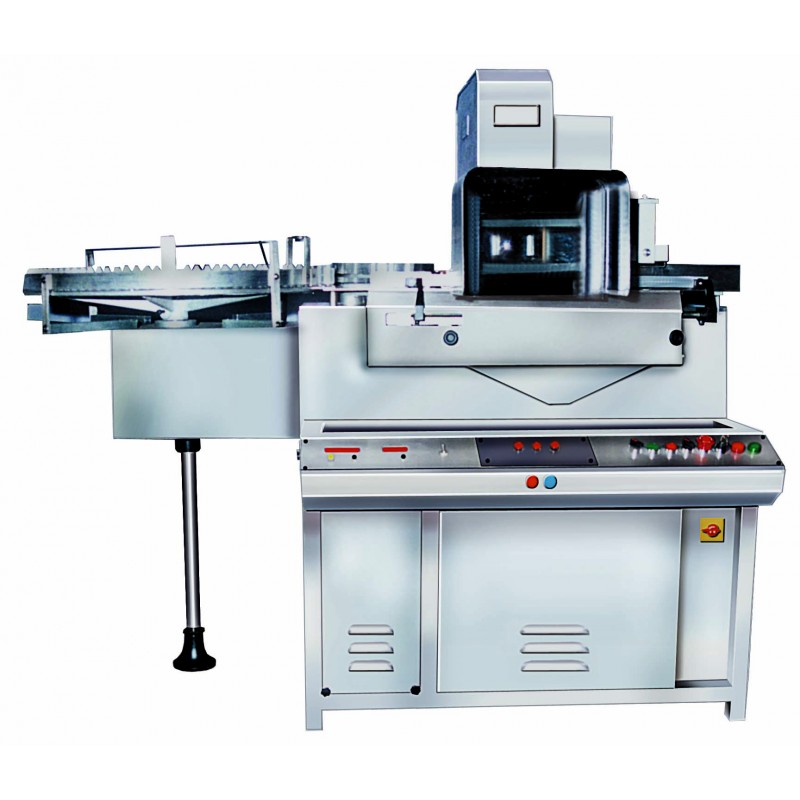
Table of Contents
Challenges in Achieving High-Accuracy Automated Visual Inspection
Automated visual inspection systems for lyophilized vials aim to replace labor-intensive manual checks, but several hurdles impede perfect accuracy. These challenges stem from the inherent nature of lyophilized products and the limitations of current technologies.
Variability in Lyophilized Vial Appearance
Lyophilized products exhibit considerable visual variability, making consistent automated detection of defects incredibly difficult. This variability arises from several sources:
- Variations in lyophilization processes: Slight changes in freeze-drying parameters can significantly alter the appearance of the final cake, leading to inconsistencies in texture, color, and structure.
- Differences in vial manufacturers: Even with the same lyophilization process, vials from different manufacturers might show variations in glass clarity, surface finish, and overall appearance. This introduces background noise that can complicate defect identification.
- Impact of formulation on visual characteristics: The specific formulation of the drug product itself influences the appearance of the lyophilized cake. Variations in particle size, concentration, and excipients can lead to different textures and appearances.
These variations complicate image analysis, demanding sophisticated algorithms capable of distinguishing natural variations from actual defects. Simple threshold-based methods often fail to provide adequate accuracy.
Distinguishing Between Acceptable Variations and Critical Defects
A major challenge lies in reliably differentiating between minor imperfections—acceptable variations within manufacturing tolerances—and critical defects that compromise product quality and patient safety. This requires a nuanced understanding of the acceptable limits for each characteristic.
- Examples of critical defects: Particulate matter, cracks in the lyophilized cake, delamination (separation of layers), and vial breakage are examples of critical defects that must be consistently identified and rejected.
- Challenges in setting acceptable thresholds: Defining precise thresholds for acceptable variations is crucial for avoiding both false positives (rejecting acceptable vials) and false negatives (accepting defective vials). This requires extensive statistical analysis and careful consideration of regulatory guidelines.
Advanced image processing techniques, coupled with machine learning models trained on large datasets of both acceptable and defective vials, are essential to address this challenge.
Limitations of Current Imaging Technologies
Current camera technologies, lighting setups, and image acquisition methods present inherent limitations that affect image quality and subsequent analysis.
- Resolution limitations: Subtle defects, such as micro-cracks or tiny particulates, might be too small to be resolved by lower-resolution cameras. High-resolution imaging is crucial for capturing these critical details.
- Sensitivity to lighting conditions: Variations in ambient lighting, shadows, and reflections can significantly impact image quality and make defect detection more challenging. Precise and controlled lighting setups are therefore vital.
- Difficulties capturing subtle defects: Some defects, like variations in cake structure or subtle color changes, might not be readily apparent in standard images. Advanced imaging techniques might be needed to highlight these subtle yet potentially crucial defects.
Advanced Technologies for Improved Automated Visual Inspection
Overcoming the challenges mentioned above requires leveraging advanced technologies to enhance the accuracy and efficiency of automated visual inspection.
Role of Artificial Intelligence (AI) and Machine Learning (ML)
AI and ML are transformative technologies offering unprecedented capabilities for automated visual inspection.
- Deep learning for defect classification: Deep learning models, particularly convolutional neural networks (CNNs), excel at analyzing images and classifying defects with high accuracy. These models can be trained on large datasets of images to learn the subtle visual characteristics that distinguish defects from acceptable variations.
- Computer vision for image analysis: Computer vision techniques provide tools for image segmentation, feature extraction, and object recognition, allowing the system to identify and isolate potential defects within the vial image.
- AI-powered algorithms for improved defect detection: AI algorithms can dynamically adapt to variations in vial appearance, improving the robustness and accuracy of defect detection even when dealing with variations in lighting, vial manufacturers, or lyophilization processes.
Advanced Image Processing Techniques
Specialized image processing techniques significantly improve the quality and analytical value of acquired images.
- Image enhancement algorithms: These algorithms can enhance contrast, sharpen edges, and reduce noise, making defects more visible and easier to identify.
- Noise reduction techniques: Noise in the image can mask subtle defects; advanced noise reduction techniques are crucial for accurate analysis.
- Advanced segmentation methods: Segmentation algorithms precisely isolate regions of interest within the image, allowing for focused analysis of the lyophilized cake and the vial itself.
Integration of Automation and Robotics
Integrating automated vial handling and robotic systems enhances the efficiency and throughput of the entire inspection process.
- Automated vial handling: Robotic systems can efficiently transfer vials from the lyophilizer to the inspection system and then to subsequent packaging or rejection stages.
- Integration with high-throughput imaging systems: Combining automated handling with high-speed imaging systems allows for rapid and continuous inspection of large batches of vials.
- Data management and reporting systems: Automated systems generate comprehensive data logs and reports, enabling traceability, quality control monitoring, and compliance with regulatory requirements.
Conclusion
Automated visual inspection of lyophilized vials is crucial for maintaining high product quality and patient safety in the pharmaceutical industry. However, achieving high accuracy requires overcoming significant challenges related to the variability of lyophilized products, the subtlety of certain defects, and the limitations of conventional imaging technologies. By integrating advanced technologies like AI, machine learning, advanced image processing, and robotics, the pharmaceutical industry can significantly improve the accuracy, efficiency, and reliability of automated visual inspection processes. Optimize your lyophilized vial inspection process by exploring advanced automated visual inspection solutions today. Contact us to learn more about cutting-edge solutions for enhanced pharmaceutical quality control.
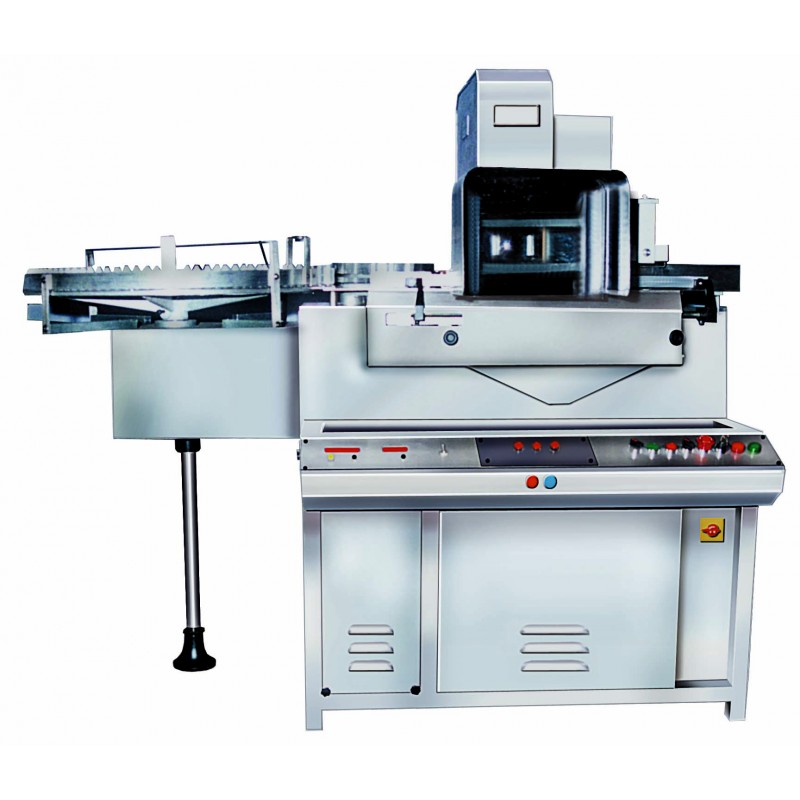
Featured Posts
-
Yankees Vs Diamondbacks Injury Report April 1 3 Series
May 11, 2025 -
The Impact Of Michael Kays Question On Juan Sotos Bat
May 11, 2025 -
Effizientes Asylmanagement Beratungsgremien Empfehlen Massnahmen Zur Kostenreduktion
May 11, 2025 -
The Benny Blanco Cheating Scandal Analyzing The Theresa Marie Connection And Fan Speculation
May 11, 2025 -
Campeonato Uruguayo Segunda Division 2025 Guia Completa De La Temporada
May 11, 2025
Latest Posts
-
Trumps Tariffs The Devastating Impact On Small Businesses
May 12, 2025 -
Lab Owner Admits Falsifying Covid 19 Test Results
May 12, 2025 -
Deadly Milwaukee Apartment Fire 4 Dead Hundreds Evacuated And Displaced
May 12, 2025 -
Documenting Floridas Alligator Population A Filming Perspective In Springs
May 12, 2025 -
Florida Spring Alligators Filming Techniques And Safety
May 12, 2025