Overcoming Hurdles In Automated Visual Inspection Of Lyophilized Drug Products
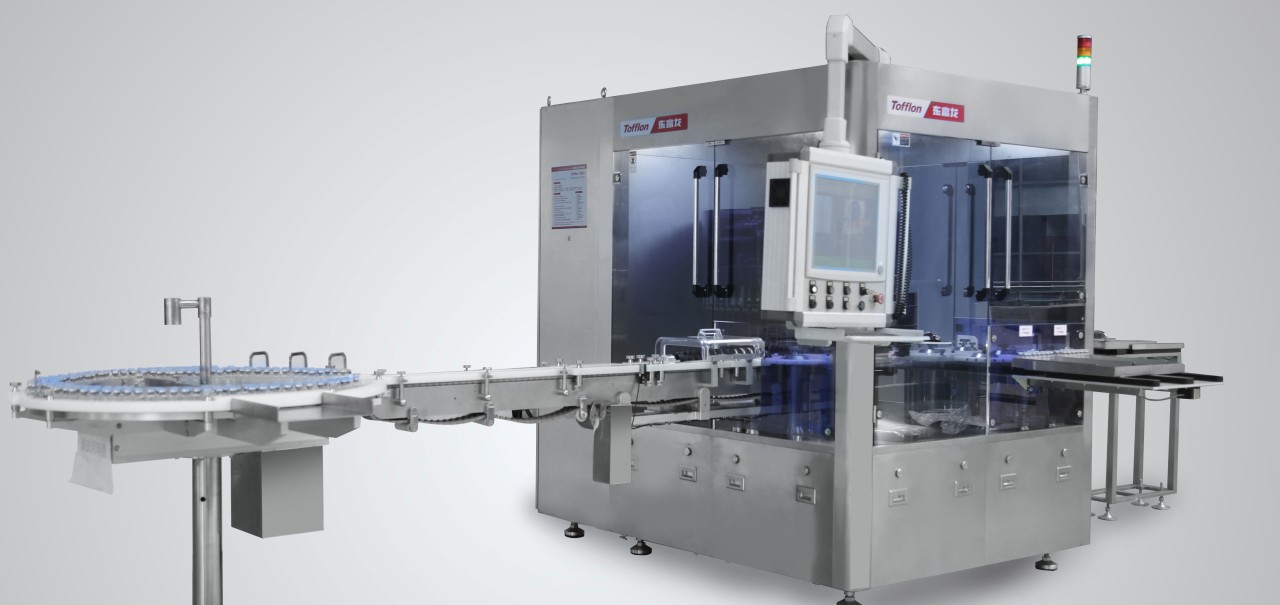
Table of Contents
Challenges in Image Acquisition for Automated Visual Inspection of Lyophilized Drugs
The acquisition of high-quality images suitable for automated analysis is a primary hurdle in the automated visual inspection of lyophilized drugs. Several factors contribute to this challenge:
Variations in Lyophilized Cake Appearance
Lyophilized drug cakes exhibit considerable natural variability in appearance. This variability makes consistent automated inspection difficult.
- Differences in cake shape, size, and color across batches: Manufacturing processes can lead to subtle, yet significant, variations in the final product's appearance.
- Presence of cracks, fissures, or other surface imperfections: These are common in lyophilized products and can be difficult to distinguish from critical defects.
- Variations in vial clarity: Slight variations in glass clarity or imperfections can interfere with image analysis.
These variations can confound automated systems, leading to false positives (rejecting good products) or false negatives (accepting defective products). Robust algorithms are needed to account for this inherent variability in cake morphology, requiring advanced image processing and computer vision techniques. Careful control of the lyophilization cycle parameters is also critical in minimizing these variations.
Lighting and Shadow Effects
Consistent and uniform illumination is paramount for accurate visual inspection. However, achieving this with lyophilized drug vials presents significant challenges.
- Difficulties in achieving uniform illumination: The vial's cylindrical shape and the often irregular shape of the lyophilized cake create variations in light reflection and shadowing.
- Shadows cast by vial geometry and cake features: These shadows can obscure defects, leading to missed detections.
- Reflections from vial surfaces: Glare and reflections from the vial's surface can further complicate image analysis.
Inconsistent lighting can obscure defects and lead to inaccurate inspection results. Advanced lighting techniques, such as structured lighting or multi-angle illumination, coupled with sophisticated shadow removal algorithms and image enhancement techniques are required to mitigate these effects. Careful design of the illumination system is crucial for the success of automated visual inspection.
Contamination Detection
Identifying and classifying contaminants is critical for ensuring product safety and efficacy. However, this can be challenging with lyophilized products.
- Identifying particulate matter, foreign bodies, and other contaminants: Automated systems must be able to detect a wide range of contaminants, from large foreign bodies to microscopic particles.
- Differentiating between acceptable variations and actual contamination: Distinguishing between acceptable variations in the lyophilized cake and actual contamination requires high resolution imaging and sophisticated image analysis algorithms.
- Sensitivity and specificity of detection: The system must be sensitive enough to detect even minute contaminants while maintaining high specificity to minimize false positives.
Accurate detection of even minute contaminants is crucial for product safety. High-resolution imaging, coupled with sophisticated image analysis techniques, is essential. This often involves machine learning algorithms trained on large datasets of images containing various types of contamination. Robust contamination control procedures throughout the manufacturing process are also necessary to minimize the occurrence of contaminants.
Developing Robust Algorithms for Automated Visual Inspection of Lyophilized Drugs
The development of robust and reliable algorithms is another significant hurdle. This requires careful consideration of various factors:
Algorithm Training and Data Requirements
The performance of any automated visual inspection system hinges on the quality and quantity of its training data.
- Need for large, diverse datasets for training: Algorithms need to be trained on a massive and diverse dataset of images representing a wide range of vial conditions, cake morphologies, and potential defects.
- Challenges in obtaining representative samples: Gathering sufficient representative samples that accurately reflect real-world variability can be challenging and time-consuming.
- Algorithm validation and verification: Rigorous validation and verification protocols are needed to ensure that the algorithm performs reliably in a production environment.
The effectiveness of automated systems depends heavily on the quality and quantity of training data. Careful selection and preparation of training data are critical. Techniques such as data augmentation can be employed to artificially increase the size and diversity of the training dataset. This usually involves the application of machine learning or deep learning techniques.
Handling Noise and Artifacts
Real-world images are rarely perfect. They often contain noise and artifacts that can interfere with defect detection.
- Minimizing the impact of noise from various sources (e.g., sensor noise, lighting artifacts): Noise reduction techniques are crucial for improving the accuracy of the inspection process.
- Distinguishing between true defects and artifacts: Algorithms must be able to reliably differentiate between actual defects and artifacts caused by noise or other factors.
- Robust algorithm design: The algorithm design should be robust enough to handle variations in image quality and lighting conditions.
Robust algorithms are needed to effectively filter out noise while retaining relevant information. Advanced image filtering techniques and sophisticated noise reduction algorithms are essential components of a successful automated visual inspection system.
Integration with Existing Manufacturing Processes
Successful implementation requires seamless integration with existing high-throughput manufacturing processes.
- Seamless integration with high-throughput systems: The automated system must be able to handle the high volume of vials processed in a typical pharmaceutical manufacturing environment.
- Data management and traceability: A robust data management system is needed to track inspection results, maintain data integrity, and ensure traceability throughout the manufacturing process.
- Compliance with regulatory requirements (e.g., 21 CFR Part 11): The system must comply with all relevant regulatory requirements for data integrity, security, and audit trails.
Successful implementation requires careful consideration of system integration and data management to ensure compliance with industry standards and regulations. This includes considerations for data security, audit trails, and electronic signatures.
Conclusion
Automated visual inspection of lyophilized drug products offers significant advantages in terms of speed, accuracy, and cost-effectiveness compared to manual methods. However, overcoming the challenges related to image acquisition, algorithm development, and system integration is crucial for successful implementation. By employing advanced imaging techniques, robust algorithms, and careful attention to data management, the pharmaceutical industry can leverage the benefits of automated visual inspection to ensure the consistent quality and safety of lyophilized drug products. Investing in research and development of improved automated visual inspection systems for lyophilized drugs will be vital to ensuring patient safety and meeting regulatory requirements in the years to come. Consider exploring the latest advancements in automated visual inspection of lyophilized drugs to enhance your quality control processes.
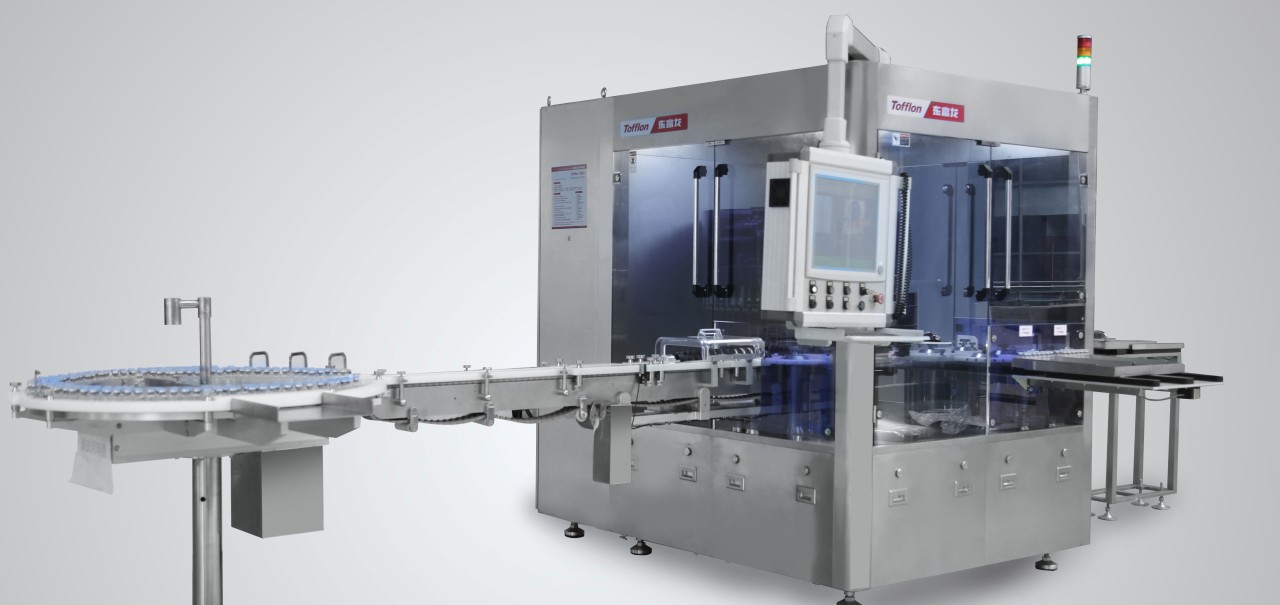
Featured Posts
-
Predicting Aaron Judges 2024 Performance Yankees Magazine Analysis
May 11, 2025 -
Reakcja Ksiecia Williama Szokujace Oswiadczenie Po Wydarzeniu Z Masazystka
May 11, 2025 -
Updated Injury Report Yankees Vs Rays May 2 4
May 11, 2025 -
Mma Torchs Top 3 Fights 5 10 And 25 Minute Showdowns
May 11, 2025 -
Astronauts Extended Space Stay Fact Checking The Cbs News Claim
May 11, 2025
Latest Posts
-
Celtics Vs Knicks Your Guide To Live Streaming And Tv Coverage
May 12, 2025 -
How To Watch Celtics Vs Knicks Free Live Stream Options And Tv Channels
May 12, 2025 -
Live Stream Celtics Vs Knicks Free Online And Tv Broadcast Details
May 12, 2025 -
Celtics Vs Knicks Game Where To Watch Live Stream And Tv Listings
May 12, 2025 -
Nba Picks Cavaliers Vs Knicks Betting Analysis And Predictions February 21
May 12, 2025