U.S. Companies Slash Costs Amidst Tariff Uncertainty
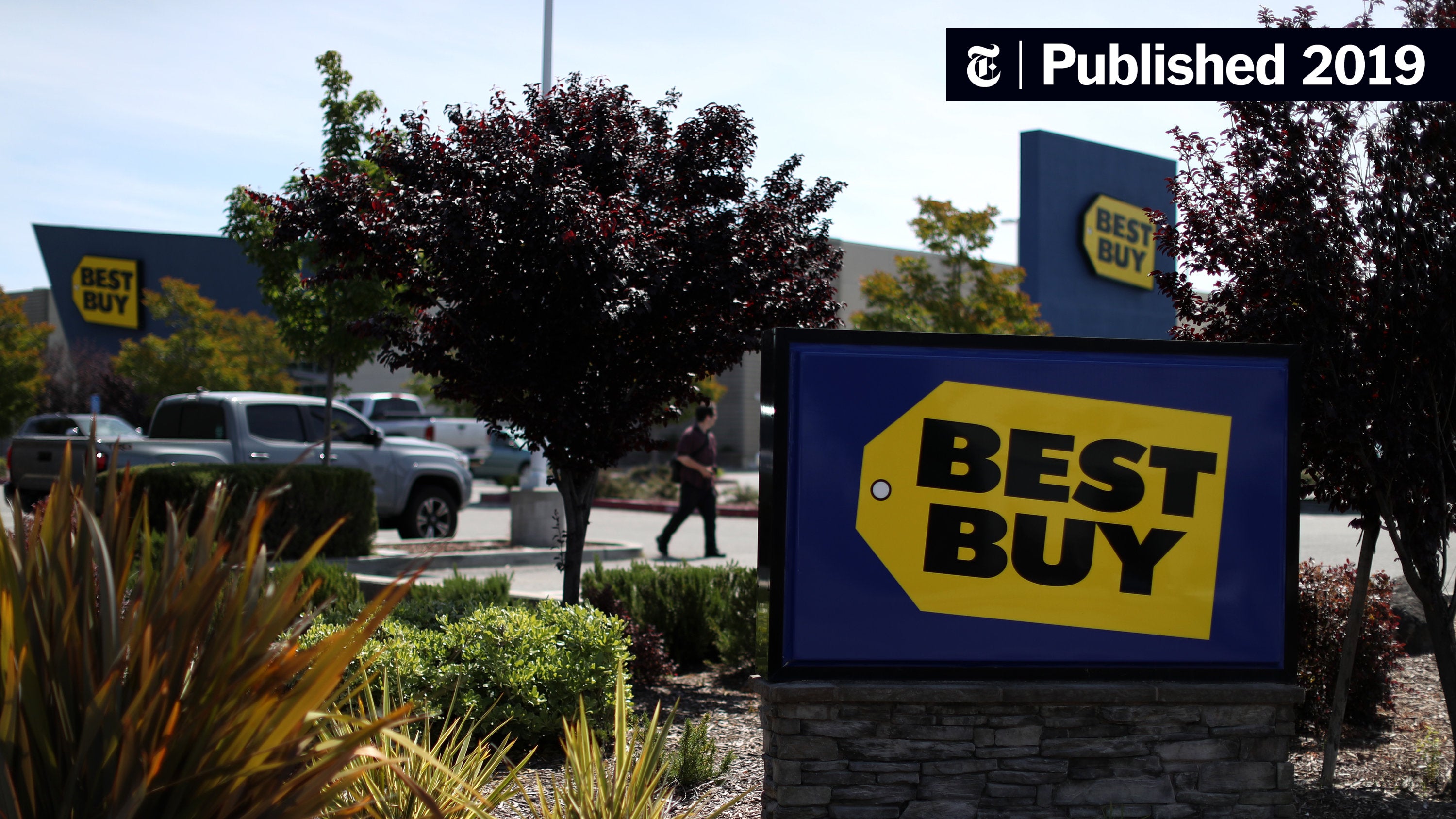
Table of Contents
Strategies for Cost Reduction in Response to Tariffs
The uncertainty created by tariffs has forced businesses to re-evaluate their operational models and implement aggressive cost-reduction strategies. Key areas of focus include supply chain restructuring, automation and technological upgrades, and inventory management optimization.
Restructuring Supply Chains
To mitigate the risks associated with tariffs, many U.S. companies are actively restructuring their supply chains. This involves a significant shift towards nearshoring and reshoring, bringing manufacturing and production closer to home, and diversifying sourcing to reduce reliance on single suppliers.
- Examples of Supply Chain Restructuring:
- Companies like Ford are investing heavily in domestic manufacturing to reduce reliance on imported parts.
- Many businesses are exploring alternative suppliers in countries with more favorable trade agreements.
- Negotiations with existing suppliers are focusing on securing more competitive pricing and longer-term contracts.
These tariff mitigation strategies are crucial for reducing vulnerability to future trade disruptions and ensuring supply chain resilience.
Automation and Technological Upgrades
Automation and technological upgrades are playing a critical role in reducing labor costs and improving efficiency. By adopting advanced technologies, companies can streamline operations and minimize the impact of tariffs on their bottom line.
- Examples of Automation and Technology Adoption:
- Increased use of robotics and automated systems in manufacturing plants.
- Implementation of AI-powered logistics and supply chain management systems for optimized delivery and reduced waste.
- Adoption of advanced software for improved inventory management and forecasting.
These cost-cutting measures not only help to offset increased input costs but also enhance overall productivity and competitiveness in the long run. Investing in technology upgrades is a key component of a broader strategy for efficiency improvements.
Inventory Management Optimization
Efficient inventory control is crucial for minimizing storage costs and preventing waste. Companies are adopting sophisticated inventory management techniques to ensure they have the right amount of materials at the right time, without excessive holding costs.
- Examples of Inventory Management Optimization:
- Implementing Just-in-Time (JIT) inventory systems to reduce warehousing needs.
- Utilizing advanced forecasting techniques to predict demand accurately and minimize overstocking.
- Improving warehouse management practices through better organization and streamlined processes.
This focus on supply chain optimization helps reduce waste reduction, directly impacting the bottom line and enhancing profitability.
Impact on Different Sectors
The impact of tariffs and the resulting cost-cutting measures vary across different sectors of the U.S. economy.
Manufacturing
The manufacturing sector has been significantly affected by tariffs, facing increased input costs and reduced competitiveness. The response has included a range of cost-cutting measures, with varying degrees of success.
- Examples of Cost-Cutting in Manufacturing:
- The steel industry has invested in automation and improved efficiency to offset increased costs of imported raw materials.
- The textile industry has focused on reshoring and exploring alternative sourcing options to reduce reliance on imported fabrics.
- Many manufacturers are actively promoting a "Made in America" message to appeal to consumers prioritizing domestically produced goods. This contributes to manufacturing cost reduction while boosting domestic production.
Retail
Retail companies are grappling with increased prices for imported goods and changing consumer behavior. Their response involves a combination of price adjustments, sourcing changes, and marketing strategies.
- Examples of Cost-Cutting in Retail:
- Retailers are adjusting prices to reflect increased input costs, while also seeking to maintain competitiveness.
- Some retailers are shifting sourcing to domestic suppliers or exploring alternative, lower-cost import sources.
- Marketing campaigns are focusing on value propositions and highlighting the benefits of certain products to maintain sales. This addresses the challenge of consumer behavior changes and impacts retail cost-cutting efforts.
Agriculture
The agricultural sector has also faced significant challenges due to tariffs, impacting both input costs and export markets. Farmers are relying on government support, diversification strategies, and exploration of new export markets.
- Examples of Cost-Cutting in Agriculture:
- Government subsidies have helped to offset some of the losses faced by farmers due to tariffs.
- Farmers are diversifying their crops to reduce reliance on single commodities affected by tariffs.
- Efforts are underway to explore and develop new export markets to reduce dependence on markets impacted by tariffs. This is directly related to the impact of agricultural tariffs.
Long-Term Implications for the U.S. Economy
The long-term implications of the cost-cutting measures driven by tariff uncertainty are complex and multifaceted. While some positive outcomes may result, such as increased domestic production and innovation, negative consequences, like job losses in some sectors and reduced consumer purchasing power, are also possible. The ultimate impact on the U.S. economic outlook remains to be seen. The economic impact of tariffs and long-term economic consequences will need careful monitoring.
Conclusion: Navigating Tariff Uncertainty and Cost Reduction Strategies
U.S. companies are employing a range of strategies to navigate the challenges presented by tariff uncertainty. These include restructuring supply chains, investing in automation, optimizing inventory management, and adapting to sector-specific challenges. The impact of U.S. Companies Slashing Costs Amidst Tariff Uncertainty is significant and far-reaching, affecting various sectors of the economy. Understanding these trends is crucial for businesses of all sizes. Learn more about developing your own effective tariff mitigation strategies today!
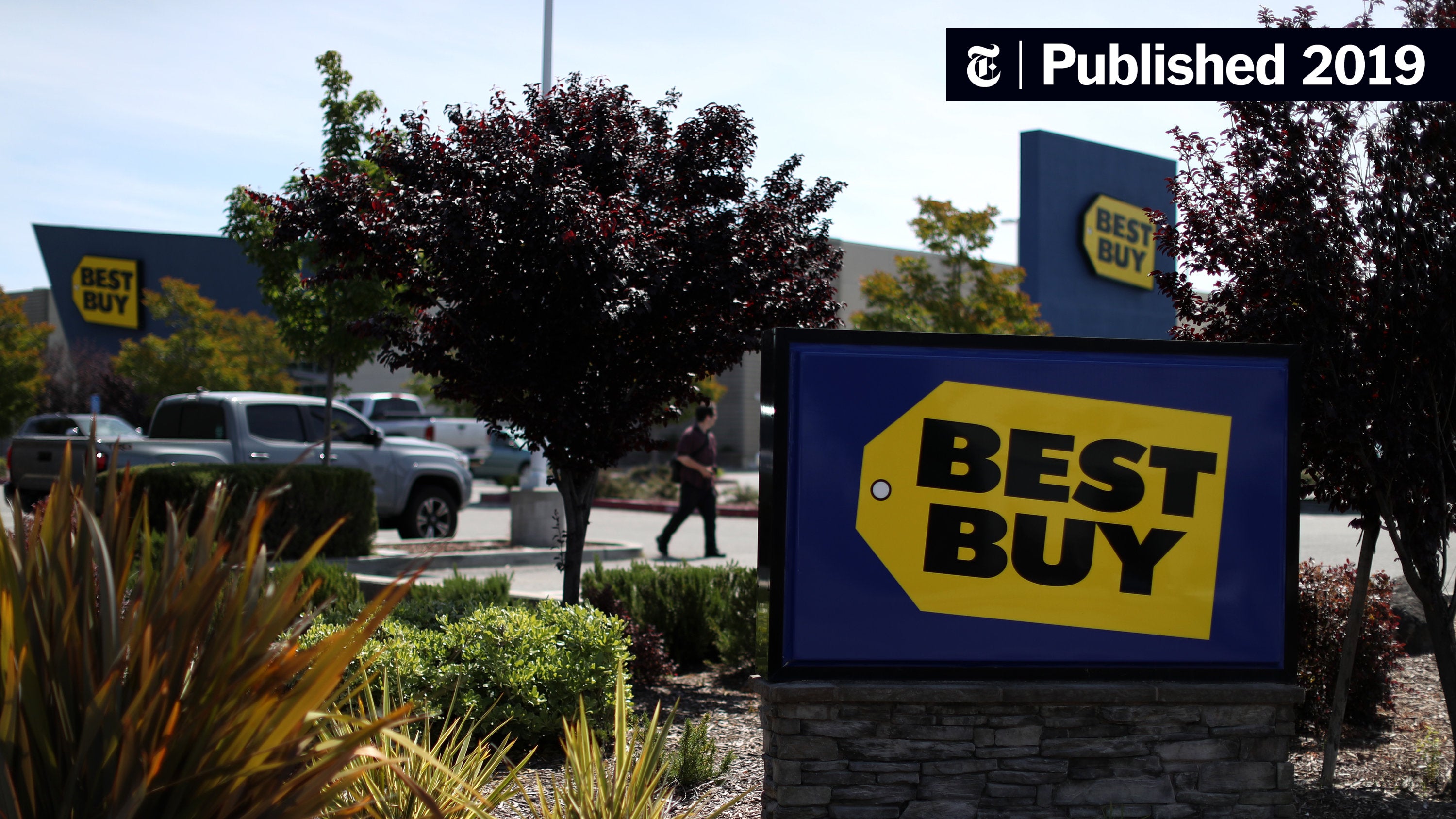
Featured Posts
-
Capital Summertime Ball 2025 How To Buy Tickets Successfully
Apr 29, 2025 -
Fatal Rock Throwing Teen Sentenced For Murder
Apr 29, 2025 -
Tylor Megills Success With The Mets Pitching Strategies And Results
Apr 29, 2025 -
Is Willie Nelsons Relentless Touring Jeopardizing His Health
Apr 29, 2025 -
Get Your Capital Summertime Ball 2025 Tickets The Ultimate Guide
Apr 29, 2025